Standard operating procedures, equipment maintenance and site design all play a role in preventing spills during fracking.
Frac companies and the oil and gas companies they work for make it a priority to prevent spills of chemicals, flowback fluid or other hydrocarbon products during fracking to protect land, vegetation, water bodies and groundwater. As a result, spills during fracking activities are relatively rare.
Spill prevention begins before the fracking equipment and materials even get to the wellsite. The trucks used to transport frac sand and chemicals are equipped with totes and brackets to securely hold their loads and prevent spills during transportation. Trucks are driven by professionals that are licensed, trained and certified to transport potentially dangerous materials and to drive in oilfield conditions.
It is in the frac company’s best interest to maintain its equipment in order to keep it in safe, reliable condition and limit costly unplanned downtime. In the same way that safe employees are productive employees, safe equipment is productive equipment. Even though equipment is well-maintained, drip trays are placed under pumping units and other equipment on location as an extra precaution to prevent any ground contamination.
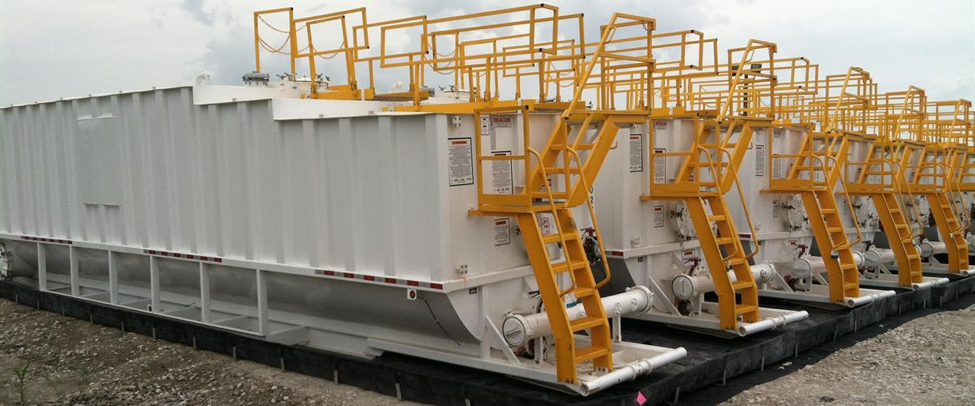
Source: PacTec Inc.
The equipment and piping used during the fracking process are inspected and pressure tested for strength and potential leaks prior to the start of each frac treatment. All equipment is assigned a maximum pressure by the manufacturer and continuous monitoring occurs during operations to ensure that pressures remain below the safety-rated level.
Improvements in frac fluid technology, such as non-toxic additives, have also helped to decrease the risk of contamination from spills. Also, old technology required powdered additives to be mixed with hydrocarbon, like diesel, to create a carrier slurry. Companies now transport powders to location to be mixed on-the-fly with water during pumping operations, eliminating the use of hydrocarbon altogether.
The chemicals required for fracking are kept inside lined secondary containment areas designed to catch any fluid releases before they can spill on location or migrate off the site. Likewise, wellsites are specifically constructed to contain any spills on the wellsite. During construction of a wellsite, the layers of soil are removed, and often separated, to ensure they are not at risk of contamination. Once drilling and fracking activities are complete, the soil is restored to its original location.
Finally, each wellsite has spill management plans in place for workers to deal with should it occur. Steps include cleaning it up, reporting it to regulators and documentation. Clean-up requirements and testing are all mandated by stringent regulations and enforced by regulators.